Inhabited module
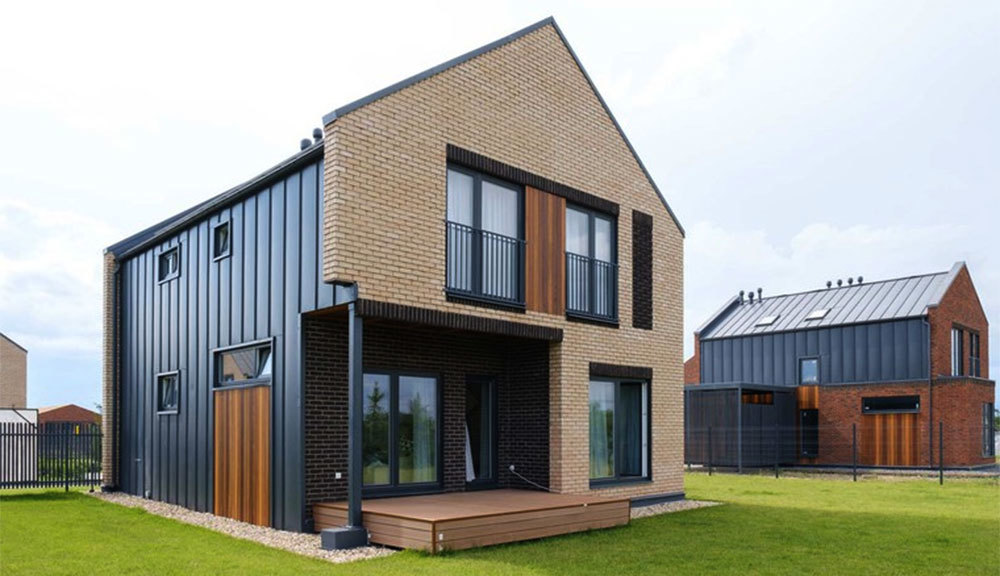
The incentive for the introduction of new technologies by developers is the need to build more, cheaper and faster, because loans are still expensive, and buyers are becoming more demanding, but not wealthier. In this regard, modular technologies are remembered more and more often. But few have managed to move beyond the discussions.
By 2030, it is expected to bring the housing commissioning in Russia to 120 million square meters per year. In 2021, 78 million square meters will be built, the Ministry of Construction forecasts, in 2022 - 80 million square meters, in 2024 - 90 million square meters. The construction should add significantly from 2027 - plus 8-12 million square meters annually. The details - at the expense of what such a breakthrough can happen - are not usually voiced, they are more about the fact that the population is in dire need of new modern housing.
Ambitious companies, building development plans, are usually guided by the following considerations: it is necessary to cut costs and reduce the cost of 1 square meter, while keeping the quality level at an acceptable level - a dubious product can no longer be sold to the modern buyer. In what the interests of developers and authorities fully coincide, so that the built could be sold, ie that housing was available to the masses. Modular construction technology is the case when everything can be achieved at once: acceleration of the production process, reduction of its cost, and higher quality.
In spring, the capital authorities started talking about it. Sergey Levkin, the head of the Department of Urban Planning Policy of Moscow, noted at that time that there are no examples of modular construction of capital objects so far. But the company "Monarch" of Sergey Ambartsumyan, the former deputy of the ex-head of the capital building complex Vladimir Resin, is closely engaged in this topic, intending to build a test modular house in the new Moscow. According to Levkin, the normative and technical base does not limit the design and construction of buildings from large-sized modules. There is a standard organization (STO) "Buildings from large-sized modules on the technology of the Combine of Innovative Technologies - Monarch. Design, manufacturing, transportation and construction. Rules, control of performance and requirements to the results of work". Also, the Ministry of Construction, Housing and Communal Services of the Russian Federation and Monarch Group of Companies have developed the second version of the draft SP "Buildings made of large-sized modules. Design Rules", which was publicly discussed in January 2021.
The purpose of the new document is to provide basic recommendations to the rules for the design and construction of buildings from large-sized modules, including the design of elements, assembly procedure, specific conditions for completing with engineering equipment, finishing and special requirements for joints that ensure the operation of the building as a whole. According to Levkin's estimation, the advantage of construction will be the reduction of the construction cycle and labor costs.
In October, in an interview with Vedomosti, Rafik Zagrutdinov, head of the Moscow Construction Department, said that modular technology, if successfully tested, could be used to build housing under the renovation program.
To meet the targets of the program, the city needs to build 1.5 million square meters of housing per year - the volume is huge. The use of modular structures will allow building faster and ensure 80% factory readiness of common areas with finishing, plumbing and electrical works.
A quest with delivery
The management of Monarch announced its plans to move towards modular housing construction in the summer of 2020. By that time, the project called "Technopolis of Modular Housebuilding" already had a two-year history and a trial module of 100 square meters for the organization of the construction headquarters, which was located in the Marushkino settlement in New Moscow. There, as an experiment, they assembled a building of 10 modules, which took five hours. "With such terms, the object pays for itself many times faster, and it is possible to pay off the bank faster, if the construction is carried out on credit funds. The maximum amount of work will take place at the enterprise, where components are produced by high-precision robotic lines. An analogy with conveyor automobile assembly, which is completed in minutes, is appropriate here," Sergey Hambartsumyan commented on the progress of the project. There are no restrictions on the number of storeys, he noted at the time. Such modules can be used to build low-rise houses as well as houses with 30 floors. Special prospects arise in case of a large order. Difficulties are related only to the delivery of modules to the site and the availability of large cranes for installation. At that time the company was negotiating with the Chinese and Italians to supply cranes of large capacity. The company called the transportation of one module from the north-west of the city to new Moscow at night a quest.
The total cost of the project "Technopolis of Modular House Building" was estimated by Hambardzumyan at 15 billion rubles. But Monarch was counting on the city's help - the approved innovation support program. By that time, the city had allocated 24.8 hectares of land to the company. The company also did not hide its ambitions to fit into the city's renovation program.
The pandemic did not interfere too much with the realization of the plans. In October, Alexander Meshcheryakov, head of the project "Combinat Innovative Technologies - Monarch", said that work is underway in New Moscow to organize an experimental building for the production of apartment modules: "In the building with an area of almost 23,000 square meters, the main construction and assembly works have been completed, gates have been installed, 80% of the external engineering networks have been completed, and the boiler room is being installed." The building should start production in the spring of 2022. Now it is 90% ready for engineering communications - gutters, sewerage, water supply, electrics and low-current systems.
But the main thing, according to Meshcheryakov, is that the design of the first 8-story experimental modular house is being finalized in parallel (there will be two such houses in total). The experimental houses will be disassembled and transported to the site in Yakovlev (New Moscow), where a low-rise residential neighborhood will be built. The first Liebherr heavy crane with a lifting capacity of 800 tons has already been delivered for the assembly of the 8-storey buildings.
The second stage of the mill construction will be the main two-storey building, finished product warehouse, checkpoint, external utilities and engineering structures. The design is currently underway. The capacity of the enterprise will be 450,000 square meters of modules per year. It is planned to complete the construction of the second stage facilities in August-September 2022, and to reach the design capacity by the end of 2024.
The finished product of the plant will be extra-large modules, 100 square meters with finishing and communications, although it is realistic to produce modules of even larger sizes - 117 square meters. m. In the future, the new technology, expect in "Monarch", will allow to deliver to the construction site not building materials, but housing with finishing and communications. It will be possible to erect a 22-storey house in less than 20 working days with better quality. The company is interested and plans to join the renovation program - to erect 1.2 million square meters of modular houses in Cheremushki when the site is ready. At present, a 3.5-story modular house has been installed and is being used as an administrative building (construction headquarters) in New Moscow.
Daniil Katrichenko, director of the Genpro design company, refers to the company's experience in the United States, where it designed a 7-story residential complex consisting of container blocks. It is being built in the city of Mesa (Arizona). The first floor, where the restaurant and parking lot are located, is built using monolithic technology, the remaining six residential floors are assembled from shipping containers with interior finishing, built-in furniture, ventilation and air conditioning systems and other communications. The container blocks themselves are manufactured at a factory in China and transported by sea, and then delivered by trucks to the construction site.
Alexey Shepel, the founder of S.Holding Corporation, reminded that modular construction was well developed in the times of the USSR. DSK-2 produced a series of modular houses, but at that time it was necessary to perform additional finishing.
According to Shepel, despite its many advantages, the technology has disadvantages. Firstly, such housing can only be categorized as mass housing. Unique architectural solutions, unusual facades - all this has nothing to do with such construction, Shepel believes. However, Fetisov disagrees with his colleague and says that the "factory" quality and precision of details will not prevent modular construction from conquering the business and even premium-class market.
Secondly, large plots of land are needed so that houses are built in a stream. If the factory stops producing modules, production immediately becomes unprofitable. In case of a large order, for example, for renovation, where the areas after the demolition of five-storey buildings have already been prepared, it will be a profitable enterprise for both the developer and the city. So the main risk, summarizes Shepel, is the absence of an order: money invested, but the order is either small or "intermittent". The cost of such a plant, he estimates, depends directly on its capacity. A plant for 150,000 square meters of housing per year can cost up to 1 billion rubles. The greater the capacity, the higher the cost due to the amount of equipment.
Natalia Krol